Power-Core™ gears have been used to upgrade the design of a latex dipping gear cassette assembly in a unique arrangement that replaces standard gears in order to meet critical performance and cleaning challenges.
The original gear box design resembled a tightly fitting cassette made with standard off-the-shelf gears. Unfortunately, as the latex material was being processed, the gears reacted with the latex material and expanded in size until the ceased turning. Cleaning required a complete disassembly of the cassette, followed by awkward and time-consuming hand scrubbing of individual components to yield less-than-satisfactory results.
In addition to requiring an easier cleaning process, the medical device manufacturer wanted longer wear-life and improved performance from the gears. Frequent cleaning and premature gear failure caused by gear swelling resulted in wear stress that resulted in system downtime and replacement on average every few months.
As part of a failure analysis, Intech provided an engineering design review that included a custom gear life calculation. Our engineering team recommended a system design modification to address performance uptime, improve wear life, and to create a user-friendly non-hazardous cleaning process.
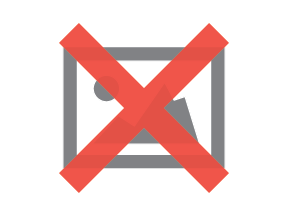
The gear box modification design features custom Intech Power-Core™ gears with a larger pitch diameter, wider face width, and an integral stainless steel shaft that extends on each side of the gear and rotates directly within the load bearing cover plates. The open sandwich design, which can be seen in this image, allows for easy cleaning.
Compared to the previously used injection molded gears which vary in size due to internal stresses and moisture absorption, the precision machined Intech Power-Core™ gears provide consistent, smooth-running operation at reduced torque. Uniform Power-Core material will not distort or change size, so individual gears can be interchanged easily without matching pre-existing gears for a uniform fit, whereas injection molded gears had to be matched to other gears in order to function.
Intech Power-Core™ gears are machined from an inert, stress-free non-hygroscopic material with integral stainless steel shaft that offers outstanding performance where corrosion, abrasion, noise, lubrication, vibration, shock, and moisture create hostile operating environments.